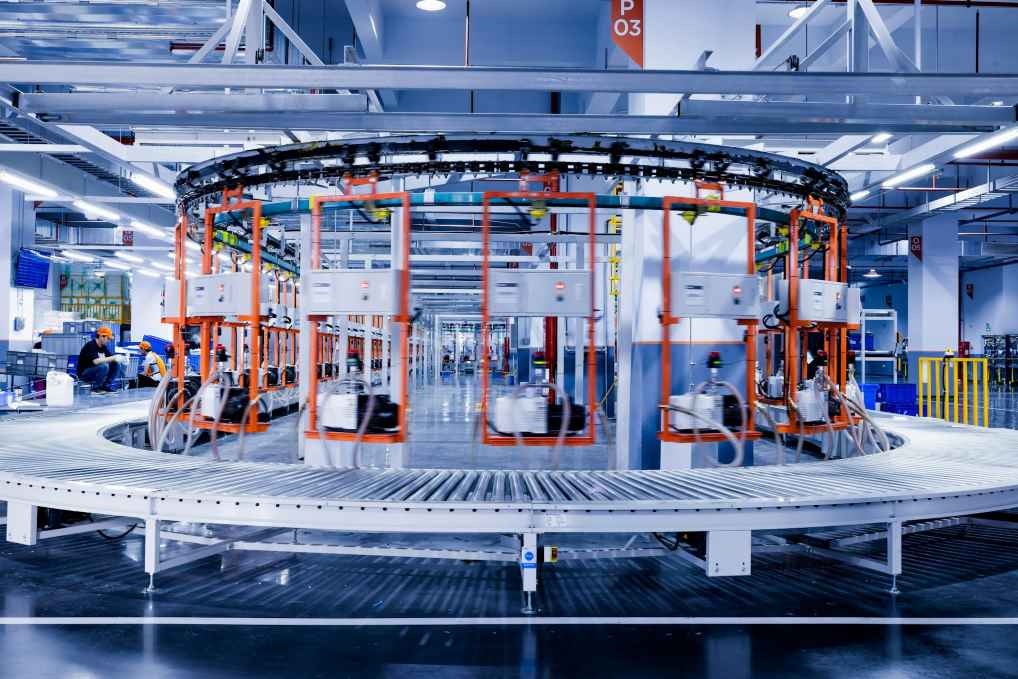
Negli ultimi anni, l’Internet of Things (IoT) ha trasformato radicalmente numerosi settori industriali. Tuttavia, uno degli ambiti in cui l’IoT industriale (IIoT – Industrial Internet of Things) ha avuto il maggiore impatto è sicuramente quello della produzione e dell’automazione industriale.
L’IIoT rappresenta una vera e propria rivoluzione, poiché consente di interconnettere macchinari, sensori, sistemi di controllo e piattaforme digitali in un ecosistema intelligente, capace di migliorare l’efficienza operativa, ridurre i costi, aumentare la sicurezza e ottimizzare le risorse.
Indice
Cos’è l’Industrial IoT?
L’Industrial Internet of Things (IIoT) rappresenta l’evoluzione tecnologica dell’Internet of Things applicata al contesto industriale. Si tratta di un ecosistema complesso e interconnesso in cui dispositivi fisici – come macchine, sensori, attuatori e controllori – comunicano tra loro e con sistemi centrali attraverso reti digitali. L’obiettivo principale dell’IIoT non è soltanto raccogliere dati, ma trasformare le informazioni acquisite in tempo reale in valore operativo concreto, migliorando prestazioni, sicurezza e produttività.
Nel cuore dell’IIoT si trova la capacità di digitalizzare i processi industriali. Questa digitalizzazione consente un passaggio dal controllo manuale o semi-automatico a una gestione automatizzata e intelligente dei sistemi produttivi.
Le tecnologie IIoT permettono alle aziende di avere una visibilità senza precedenti sui loro impianti e operazioni, creando un ambiente in cui ogni elemento del sistema produttivo diventa parte attiva di una rete dinamica e adattiva.
Ciò che distingue l’IIoT dal semplice concetto di automazione tradizionale è la connessione costante tra il mondo fisico e quello digitale. Ogni componente industriale, una volta dotato di sensori e capacità di comunicazione, si trasforma in una fonte attiva di dati e può dialogare con software avanzati per l’elaborazione, l’analisi e la visualizzazione delle informazioni.
L’IIoT permette quindi di prendere decisioni più rapide e basate su dati concreti, abilitando approcci come la manutenzione predittiva, la pianificazione intelligente e l’ottimizzazione continua dei processi.
L’automazione industriale: una nuova era con l’IIoT
L’avvento dell’Industrial IoT ha segnato una profonda trasformazione dell’automazione industriale, spingendola oltre i limiti dell’automazione tradizionale basata su logiche rigide e sistemi chiusi.
In passato, l’automazione era fortemente vincolata a configurazioni predefinite, dove l’adattabilità e la capacità di reazione ai cambiamenti in tempo reale erano fortemente limitate. Con l’integrazione dell’IIoT, invece, i sistemi produttivi acquisiscono una nuova dimensione: diventano intelligenti, reattivi e, soprattutto, capaci di apprendere.
Le fabbriche moderne si trasformano in ecosistemi digitali in cui ogni macchina è connessa e ogni processo è monitorato in tempo reale. La produzione non è più una sequenza statica di operazioni, ma un flusso dinamico in continua evoluzione.
Grazie ai dati raccolti da sensori e dispositivi intelligenti, è possibile conoscere esattamente cosa accade in ogni istante della catena produttiva, individuando anomalie, inefficienze o opportunità di ottimizzazione con una precisione senza precedenti.
L’automazione diventa così proattiva: non si limita a eseguire ordini, ma è in grado di adattarsi autonomamente alle condizioni operative, di anticipare problemi prima che si manifestino e di suggerire modifiche ai parametri di processo per migliorare la qualità o l’efficienza.
Questo livello di autonomia è reso possibile dall’integrazione dell’analisi predittiva, del machine learning e di modelli digitali come il gemello digitale, che simulano il comportamento reale degli impianti e consentono di testare scenari senza fermare la produzione.
Inoltre, l’IIoT facilita una nuova forma di collaborazione tra uomo e macchina. Gli operatori umani, supportati da interfacce intuitive e dati contestualizzati, possono prendere decisioni più rapide e informate. Le tecnologie wearable e la realtà aumentata stanno ridefinendo il modo in cui il personale interagisce con gli ambienti industriali, migliorando l’ergonomia, la sicurezza e la produttività.
Questa nuova era dell’automazione non è solo una questione tecnologica, ma una vera e propria rivoluzione culturale e organizzativa. Richiede una ridefinizione dei processi aziendali, una maggiore integrazione tra reparti, e una strategia chiara per l’adozione della digitalizzazione a tutti i livelli dell’impresa.
Tecnologie chiave dell’IIoT nella produzione
Alla base dell’Industrial IoT si trovano una serie di tecnologie abilitanti che rendono possibile la trasformazione digitale dei processi produttivi. Queste tecnologie, benché diverse tra loro per natura e funzione, agiscono in sinergia per creare un ambiente industriale completamente interconnesso e orientato all’intelligenza operativa.
Un ruolo cruciale è svolto dai sensori intelligenti, i quali rappresentano i sensi del sistema IIoT. Essi rilevano dati ambientali e operativi – come vibrazioni, temperatura, corrente elettrica, livelli di pressione o presenza di anomalie – trasformandoli in segnali digitali trasmessi in rete.
La miniaturizzazione, la maggiore precisione e la capacità di auto-diagnosi rendono questi dispositivi fondamentali per acquisire dati affidabili e dettagliati in tempo reale.
A fianco dei sensori, entra in gioco il sistema di elaborazione dati, che può avvenire sia localmente (attraverso edge computing) che in ambienti remoti (tramite cloud computing). Il computing edge consente reazioni immediate direttamente vicino alla fonte dei dati, riducendo la latenza e garantendo una maggiore resilienza nei processi critici.
Il cloud, invece, permette di centralizzare e analizzare grandi volumi di dati, applicando algoritmi di machine learning per identificare pattern complessi, prevedere guasti, o suggerire strategie di miglioramento.
La connettività è l’altro pilastro fondamentale dell’IIoT. Senza una comunicazione affidabile, scalabile e sicura tra dispositivi, l’intero ecosistema crollerebbe. Protocolli industriali moderni come MQTT e OPC UA, uniti a reti avanzate come 5G industriale o LoRaWAN per trasmissioni a lunga distanza, permettono di garantire uno scambio continuo di informazioni anche in ambienti difficili, con interferenze e criticità operative.
Sulla base di questi dati e grazie all’integrazione di intelligenza artificiale, i sistemi possono andare oltre la semplice automazione e adottare comportamenti predittivi o addirittura autonomi. L’AI interpreta i dati, apprende dai risultati passati, e propone decisioni basate su evidenze numeriche. Ciò è particolarmente utile nei sistemi di controllo adattivo, nella gestione energetica e nell’ottimizzazione multi-obiettivo dei processi.
Infine, una delle innovazioni più rivoluzionarie è il concetto di digital twin, ovvero la replica digitale di una macchina, linea di produzione o intero impianto. Questo modello virtuale si aggiorna in tempo reale sulla base dei dati raccolti sul campo e permette simulazioni avanzate, previsioni di comportamento, e addirittura il training di operatori in ambienti virtuali immersivi.
Tutte queste tecnologie, integrate tra loro, non solo potenziano le capacità operative delle aziende manifatturiere, ma ne cambiano radicalmente il modello di business, aprendo la strada a servizi data-driven, produzioni personalizzate e nuovi paradigmi di efficienza sostenibile.
Vantaggi dell’IIoT per l’automazione industriale
L’adozione dell’Industrial IoT nella produzione rappresenta una leva strategica capace di generare vantaggi su più livelli, trasformando radicalmente le modalità con cui le imprese gestiscono i propri impianti, risorse e decisioni operative. Uno dei principali benefici risiede nella capacità di incrementare l’efficienza operativa in maniera continua e automatizzata.
Grazie all’interconnessione tra sensori, macchinari e software intelligenti, le aziende possono monitorare e regolare i processi produttivi in tempo reale, intervenendo tempestivamente su eventuali deviazioni dagli standard o inefficienze produttive. Questo tipo di intervento dinamico permette di ottimizzare l’utilizzo delle risorse disponibili, dai materiali all’energia, riducendo sprechi e costi non necessari.
L’IIoT consente anche una maggiore flessibilità nei processi produttivi, un aspetto sempre più cruciale in un mercato globale caratterizzato da una domanda variabile e personalizzata.
Le fabbriche dotate di sistemi intelligenti possono riconfigurare rapidamente le linee produttive, adattandole a nuovi design, varianti di prodotto o lotti su misura, senza richiedere lunghe interruzioni o complessi interventi manuali. In questo modo, le imprese diventano più agili, pronte a rispondere alle esigenze del mercato e a sfruttare nuove opportunità commerciali.
Un ulteriore vantaggio significativo è la riduzione dei costi operativi, che si ottiene non solo attraverso un uso più efficiente dell’energia e dei materiali, ma anche grazie alla riduzione delle interruzioni non programmate. L’analisi predittiva e la manutenzione intelligente permettono di evitare guasti improvvisi, programmando gli interventi in momenti strategici, minimizzando i fermi e aumentando la disponibilità delle linee produttive.
Non meno importante è il miglioramento della qualità del prodotto. I sistemi IIoT monitorano in maniera continua e dettagliata ogni fase del ciclo produttivo, rilevando anche le più piccole variazioni nei parametri critici. Questo permette un controllo qualità in tempo reale, la riduzione degli scarti e una tracciabilità completa di ogni singolo componente o lotto, migliorando la conformità alle normative e la fiducia dei clienti.
Infine, l’IIoT offre strumenti avanzati per il miglioramento della sicurezza e della salute sul lavoro. I sensori ambientali e di prossimità possono rilevare condizioni potenzialmente pericolose prima che diventino un rischio concreto, attivando allarmi, blocchi automatici o avvisi agli operatori. In parallelo, la raccolta e analisi dei dati comportamentali consente di identificare abitudini operative scorrette, promuovendo una cultura della sicurezza basata sui dati.
Sfide e criticità dell’adozione dell’IIoT
Sebbene l’adozione dell’IIoT offra numerosi vantaggi, il percorso verso una produzione digitalizzata non è privo di ostacoli e criticità. Una delle principali preoccupazioni riguarda la sicurezza informatica, che diventa un aspetto centrale in un ambiente in cui ogni macchina, sensore e sistema gestionale è connesso a una rete.
L’aumento della superficie di attacco rende gli impianti vulnerabili a intrusioni esterne, atti di sabotaggio o furti di dati industriali. Questo comporta la necessità di adottare strategie di cybersecurity avanzate, che includano protezioni a più livelli, aggiornamenti costanti dei sistemi, e soprattutto una gestione rigorosa degli accessi e dei permessi.
Un’altra sfida significativa è rappresentata dalla mancanza di compatibilità tra le tecnologie esistenti e quelle di nuova generazione. Molti impianti industriali, soprattutto quelli più datati, utilizzano infrastrutture legacy che non sono facilmente integrabili con i sistemi IoT moderni. Questo scenario richiede un approccio ibrido, in cui le nuove tecnologie devono poter coesistere con quelle tradizionali, attraverso l’adozione di protocolli standard, gateway intelligenti e soluzioni middleware capaci di favorire l’interoperabilità.
La gestione dei dati rappresenta un ulteriore elemento critico. I sistemi IIoT generano una quantità enorme di informazioni, il che può mettere sotto pressione le infrastrutture IT aziendali, sia dal punto di vista della capacità di elaborazione che dello stoccaggio. È fondamentale, quindi, disporre di una strategia strutturata per la raccolta, la filtrazione, l’analisi e l’archiviazione dei dati, con l’obiettivo di trasformare i dati grezzi in insight utili per il business, evitando al contempo la cosiddetta “data overload”.
Non meno importante è la questione della formazione del personale. L’adozione dell’IIoT richiede nuove competenze tecniche, come la conoscenza di linguaggi di programmazione, strumenti di analisi dei dati e piattaforme cloud. Le aziende devono quindi investire in formazione continua, aggiornamento delle competenze e creazione di team multidisciplinari in grado di integrare conoscenze ingegneristiche, informatiche e gestionali.
Infine, non si può sottovalutare l’impatto culturale e organizzativo che una trasformazione così profonda comporta. L’introduzione dell’IIoT cambia radicalmente il modo in cui si prendono decisioni, si progettano i processi e si interagisce con la tecnologia. Serve un cambiamento di mentalità a tutti i livelli aziendali, che valorizzi l’innovazione, la sperimentazione e l’analisi basata sui dati.
Casi d’uso reali
L’implementazione dell’Industrial IoT è già oggi una realtà concreta in molteplici settori industriali, dimostrando il suo potenziale trasformativo attraverso casi d’uso ben documentati. Nel settore automotive, per esempio, le grandi case automobilistiche stanno adottando sistemi IIoT per monitorare in tempo reale ogni fase della linea di montaggio.
Ogni veicolo viene tracciato dal momento dell’assemblaggio fino all’uscita dalla fabbrica, con dati raccolti su saldature, verniciatura, elettronica e test funzionali. L’introduzione di robot collaborativi e sistemi intelligenti ha permesso una riduzione drastica dei difetti, un incremento della produttività e una capacità di personalizzazione del prodotto impensabile fino a pochi anni fa.
Nell’industria alimentare, l’IIoT sta rivoluzionando la tracciabilità e la sicurezza dei prodotti. I sensori monitorano la temperatura, l’umidità, i livelli di contaminazione e le condizioni igieniche delle linee di produzione, permettendo un controllo rigoroso della qualità e della conformità sanitaria. Grazie ai sistemi di visione artificiale e agli algoritmi predittivi, è possibile intervenire istantaneamente su deviazioni nei parametri critici, garantendo la massima affidabilità e riducendo gli sprechi alimentari.
Un altro esempio significativo si trova nella manifattura pesante, dove le aziende devono far fronte all’usura rapida degli impianti e alla necessità di continuità operativa. In questi ambienti, l’IIoT consente di monitorare le vibrazioni, le temperature dei cuscinetti, le pressioni idrauliche e altre variabili cruciali per la salute degli asset. L’analisi di questi dati consente di pianificare interventi manutentivi solo quando realmente necessari, riducendo al minimo i fermi macchina e ottimizzando i costi di manutenzione.
In ciascuno di questi settori, l’adozione dell’IIoT ha portato a risultati misurabili: minori costi, maggiore efficienza, miglior qualità del prodotto e una reattività superiore rispetto ai cambiamenti di mercato o alle emergenze operative.
Il futuro: verso la fabbrica intelligente (Smart Factory)
Guardando al futuro, l’Industrial IoT non è solo una tecnologia emergente, ma una componente centrale di un più ampio paradigma industriale: quello della fabbrica intelligente, o “Smart Factory”. In questo nuovo modello produttivo, l’integrazione tra macchine, dati e intelligenza artificiale raggiunge un livello tale da consentire processi decisionali completamente autonomi, adattivi e ottimizzati.
Le fabbriche intelligenti sono ambienti in cui ogni componente, umano o digitale, lavora in sinergia per massimizzare la qualità, la produttività e la sostenibilità.
La direzione è quella verso una produzione data-driven, dove ogni azione è guidata da informazioni raccolte, analizzate e messe in relazione con obiettivi strategici. Le tecnologie emergenti come la robotica collaborativa, la blockchain per la tracciabilità, la realtà aumentata per il supporto agli operatori e l’integrazione con l’intelligenza artificiale permetteranno alle aziende di affrontare sfide complesse con una flessibilità e una precisione senza precedenti.
La personalizzazione di massa diventerà uno standard, grazie a linee produttive riconfigurabili in tempo reale e a un controllo totale del ciclo di vita del prodotto. I clienti finali potranno richiedere prodotti su misura, realizzati con la stessa efficienza e velocità di una produzione di massa.
Allo stesso tempo, la sostenibilità ambientale diventerà un vantaggio competitivo reale, poiché l’IIoT permetterà di ottimizzare i consumi energetici, ridurre gli scarti e monitorare l’impatto ambientale in ogni fase produttiva.
La fabbrica del futuro sarà, in definitiva, una rete intelligente di entità connesse, capaci di auto-gestirsi, comunicare in modo continuo e adattarsi in tempo reale. Non si tratterà più solo di “fare meglio” ciò che già si fa, ma di ripensare completamente il modo in cui si produce, si innova e si compete. In questo scenario, l’Industrial IoT non è un’opzione, ma un requisito fondamentale per rimanere rilevanti nel panorama industriale globale.
Conclusione
L’Industrial IoT rappresenta una trasformazione epocale per l’industria manifatturiera e oltre. L’automazione della produzione non è più solo una questione di efficienza meccanica, ma diventa una sfida di intelligenza digitale.
Le aziende che sapranno investire in infrastrutture IIoT, competenze e sicurezza, saranno in grado di competere su scala globale, rispondere più rapidamente alle esigenze del mercato e costruire un futuro produttivo più sostenibile, efficiente e resiliente.
In un mondo in cui i dati sono il nuovo petrolio, l’IIoT è il motore che trasforma questi dati in valore industriale reale.
Internet delle Cose (IoT)
- Cos’è l’Internet delle cose (IoT) e come funziona
- Casa intelligente: Dispositivi IoT e il loro utilizzo
- Sicurezza nell’internet delle cose (IoT): Rischi e protezione
- Industrial IoT: L’automazione della produzione nell’era digitale
- Come l’IoT sta cambiando la vita quotidiana
- Protocolli IoT: MQTT, CoAP e altri – Il cuore invisibile dell’Internet delle Cose
- Edge Computing: Il futuro decentrato dell’internet delle cose (IoT)
- IoT (Internet delle cose) in agricoltura
- Piattaforme e strumenti per lo sviluppo dell’IoT
- Scalabilità delle soluzioni IoT nei sistemi industriali